Weiler Consumable Productivity Program (WCP) Improves Total Operating Costs
When was the last time you measured the total operating costs associated with your abrasive consumables?
Inefficiencies in metal fabrication production can lead to unnecessary downtime, labor constraints, bottlenecks, and even overspending.
WCP: A Program That Quantifies Improvements
From foundry cleaning rooms to fab shops, there is a strong desire to find cost savings and productivity improvements, but most lack the resources to optimize their cutting and grinding operations.
The Weiler Consumable Productivity (WCP) program helps facilities find cost and time savings in their fabrication operations when they don’t have the resources or process to quantify results. WCP is a proven process that effectively and efficiently measures real-world data. This program takes minimal effort to deploy in your facility because abrasives experts implement it.
Through a simple yet effective approach, the WCP program identifies improvements by evaluating your operations and how abrasives are used in your facility.
The Weiler Approach
WCP Customer Testimonial
Weiler used WCP at JC Steele to eliminate a production thread and increase productivity.
WCP in Action
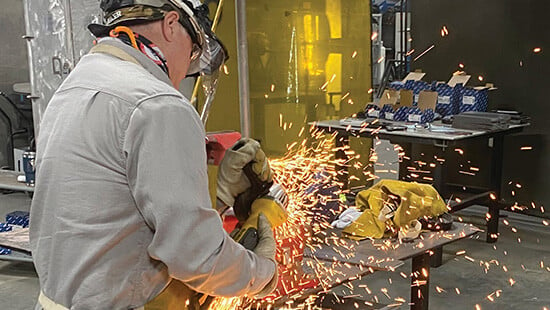
Shipbuilding Case Study
Weiler helps shipbuilder solve application challenge to meet government back gouging requirements.
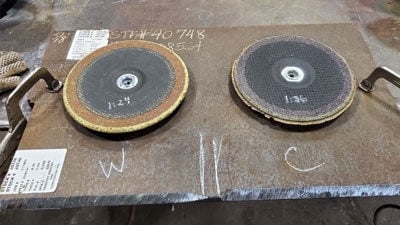
Pressure Vessel Case Study
Tiger grinding wheels deliver longer life and a faster cut rate, resulting in $9,000 cost savings for a tank fabricator.
The WCP Program Brings Real Value to Our End Users
"We don’t just swap out abrasives. We look at the process and find a better way to do it. Matching the right product to the shop’s equipment and materials is key. If we can eliminate steps in the production process, we can provide even greater value to our customers."
Director of End User Sales, Weiler Abrasives.