REDUCE COSTS AND ENHANCE EFFICIENCY IN CUTTING AND GRINDING BY USING DATA
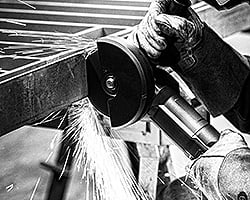
Reduce Costs and Enhance Efficiency in Cutting and Grinding by Using Data
Manufacturing facilities looking to reduce costs and improve production should consider all aspects of their operation, including the cutting and grinding process, to find savings.
Some companies may view abrasive products as interchangeable consumables that are a small piece of the overall production process. However, choosing the right abrasive for the application and using it properly can substantially impact production upstream and downstream. Abrasives affect user efficiency, labor costs, and overall quality of the finished part. Therefore, finding efficiencies with a change of abrasives can result in significant time and cost savings.
Analyzing data from the manufacturing process can help ensure that companies choose the right abrasive products to optimize efficiency and savings.
How Do Abrasive Products Affect the Operation?
Choosing an abrasive based solely on the initial product price may increase costs in the long run. Using a cheaper wheel or the wrong wheel for the job can affect throughput, downtime, and productivity. Labor is typically the largest expense in any operation, so any change that reduces downtime and improves productivity can have a positive ripple effect throughout the entire production operation.
When working with any type of abrasive product (including grinding wheels, flap discs, or cut-off wheels), the product can affect the overall operation in several ways. Here are a few common challenges related to abrasive products that can add time and costs:
- Unnecessary downtime for wheel changeover: If the wrong abrasive for the application is used, the product may not perform as needed. This may cause improper wheel use, premature wheel failure, or simply more frequent wheel changeover. The added downtime can create bottlenecks and labor inefficiency upstream and downstream of the cutting and grinding process. Minimizing wheel changeover reduces downtime and improves efficiency, allowing companies to reallocate employee time elsewhere in the facility to boost throughput or add another workstation.
Measuring a grinding wheel to collect data can help operations determine if the wheel is being used to its optimal life.
- Reduced product life: Using the incorrect abrasive for the job or the material can also reduce expected wheel life. This forces users to change the wheel more frequently. It also increases costs because more products are being used. Choosing the correct abrasive helps improve efficiency, so the wheel can be used to its full life. Ultimately, this uses fewer abrasives and saves labor time.
- Too much rework: Many manufactured products must be inspected or tested to meet certain customer specifications. If the finished product does not meet the standards, it requires rework or the part may be scrapped entirely. Rework adds material expenses and labor time, driving up costs. Choosing the appropriate abrasive for cutting and grinding can help operations minimize rework and ensure quality results.
Conducting a Comprehensive Review
If a company could shave six minutes off every hour in the cutting and grinding process, what would that equal in savings for the entire year? There is a way to find out. Measuring the total operating costs associated with abrasive consumables can help identify efficiency gains and time savings. However, it is important to look at the entire operation and all the factors involved with the abrasives process to get the full picture. Even a small change in one part of the operation can have ripple effects throughout the entire production line.
One example of this is poor part fit-up in material preparation. When this happens, employees must spend additional time downstream to correct the poor fit-up. They may need to use extra filler metal to fill the gap. Using a standard cutting wheel to prepare material for production can potentially leave burrs and an uneven cut. Switching to an ultra-thin cutting wheel delivers faster, smoother, and cleaner cuts. This allows workers to spend less time on burr removal and possibly use less filler metal to complete the weld.
To ensure a company is looking broadly at all aspects of the production process, it is a good idea to partner with an abrasives manufacturer to conduct a comprehensive review. The evaluation should go beyond simply swapping out the current abrasive for something else since the problem may stem from elsewhere in the operation. Be sure to consider all factors, from the angle of the tool to the work environment. The analysis should also examine the operation’s challenges, goals, and measures for success. Taking all this information into account helps ensure a comprehensive improvement plan.
Real-world Examples of Savings
The Weiler Consumable Productivity (WCP) program from Weiler Abrasives helps facilities save money in their fabrication operations. The process efficiently measures data and requires minimal effort to deploy in a facility because abrasives experts implement it.
The program can help companies identify improvements by evaluating the overall operation and how abrasives are used in a facility. An on-site assessment by abrasive experts allows them to learn firsthand about the production process and collect data on how abrasives are used. A baseline is established by capturing data on the current process. That is followed by testing of the current process and abrasives. The experts then calculate the estimated annual savings that a product change could provide based on labor, time, and consumable consumption. They use data to build a plan to eliminate inefficiencies in production by using the best abrasives for the application — and potentially improve productivity and throughput.
In one example, Weiler Abrasives used the WCP evaluation process to help Fibmarkt, a major player in heavy equipment fabrication, achieve big savings in their metalworking operations.
In one example, Weiler Abrasives used the evaluation process to help Fibmarkt, a major player in heavy equipment fabrication, achieve big savings in their metalworking operations. An expert team visited the Fibmarkt site for a thorough analysis of their production processes and abrasive product use, testing cutting and grinding wheels and comparing time of the cut and life of the abrasives. The experts identified significant cost reductions in consumable abrasives and labor, boosting Fibmarkt’s productivity and profits. The abrasives change provided the customer an expected annual savings of more than 86.000 EUR.
Optimize Abrasive Operations With Data
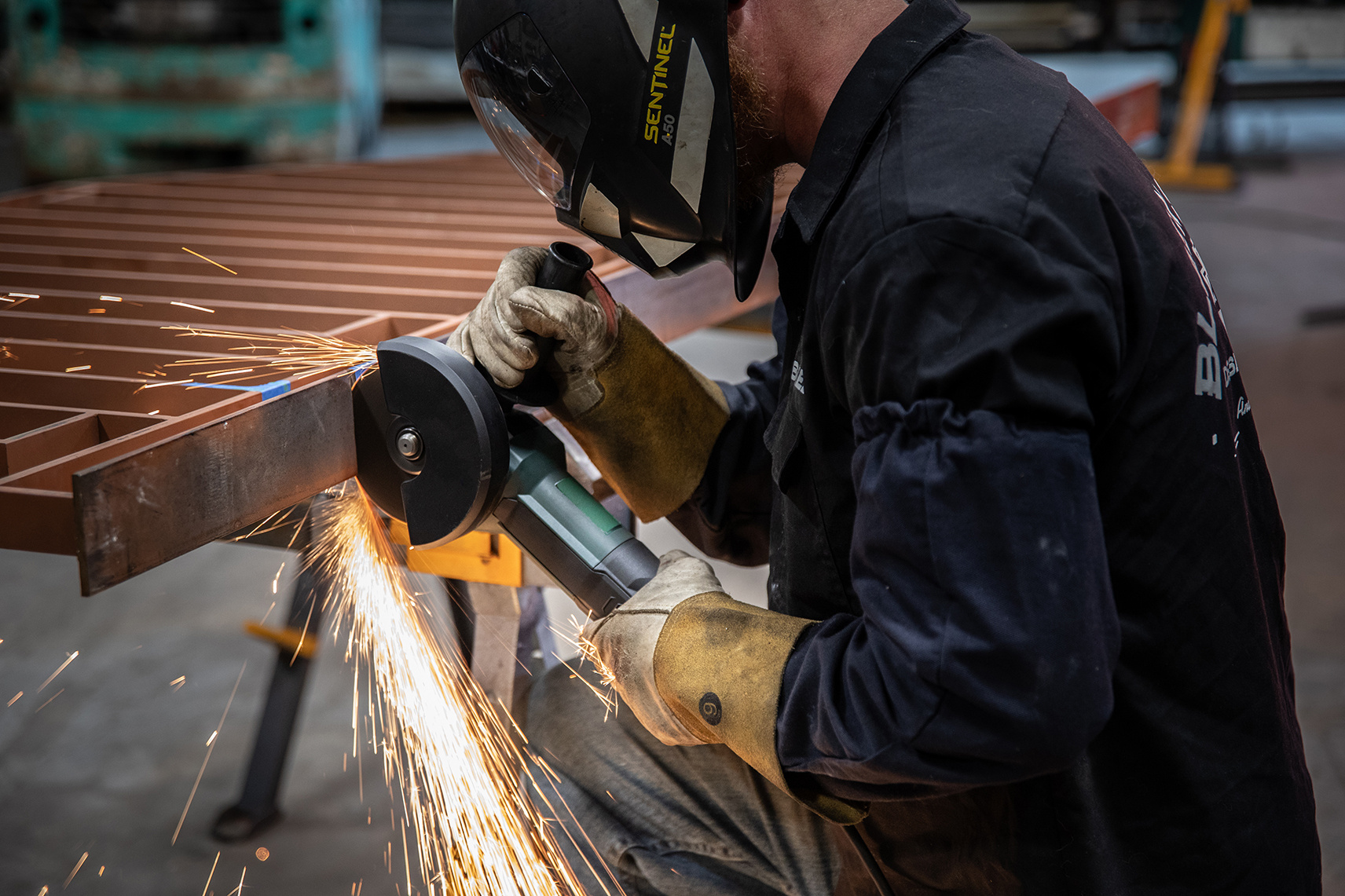
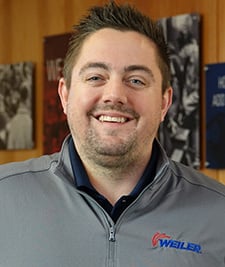
John Hobbs
Director of sales,
Weiler Abrasives
The Weiler consumable productivity program (WPC):
The Weiler Consumable Productivity (WCP) program specializes in enhancing cutting operations in fabrication facilities, particularly where there's a lack of resources or methods to measure outcomes. WCP stands as a tested approach, focusing on efficiency, and providing real-world data to pinpoint opportunities for cost and time reductions.