Weiler Process Solutions: Bringing Process, Expertise, and Partnership Together.
In today's competitive manufacturing landscape, improving high-volume production processes is crucial for a business to meet the demands of its customers and achieve profitability goals. When it comes to surface conditioning, having a partner you trust is crucial to realizing your continuous improvement objectives.
The Weiler Process Solutions (WPS) program delivers customized solutions based on your specific application needs. The program leverages the latest technology and on-site technical expertise to optimize high-volume production manufacturing processes for customers. WPS makes it easier to achieve your cost savings and productivity improvement goals.
WPS is designed to identify opportunities to make improvements that will immediately impact your business by driving down the total cost per part, increasing productivity, or both. Through the WPS program, Weiler Abrasives brings technical support and experience to your facility and works with your team to develop a tailored solution that achieves your objectives.
The Benefits of WPS
When you partner with Weiler Abrasives, our goal is to understand your objectives and offer a solution to achieve them holistically and economically. Whether investing in new machines or optimizing what you have, WPS helps bridge the gap between your current capabilities and your operational objectives. Helping you get from where you are to where you want to be.
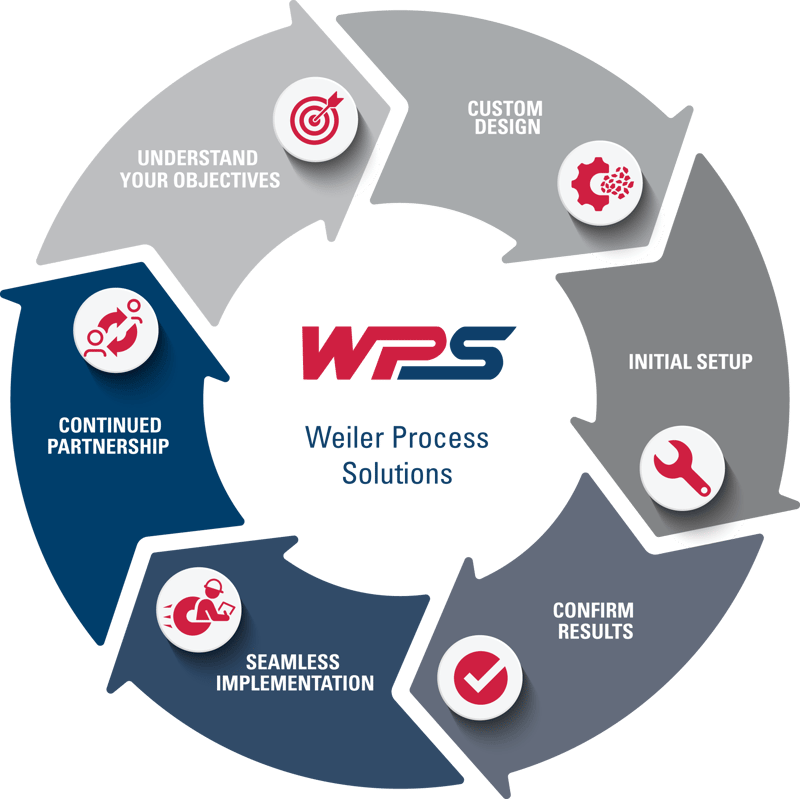
WPS Process Includes:
-
- Understanding Your Objectives: We start by understanding your unique priorities and goals.
-
Custom Design: Our expert team designs tailored solutions to meet your specific needs.
-
Initial Setup: Machine parameters are optimized for the abrasive or brush and an initial test is performed to confirm design.
-
Confirmation of Results: An extended check test confirms the results in production.
-
Seamless Implementation: Develop a conversion plan for a smooth implementation of products and improvements in your operations.
-
Continued Partnership: Regular touchpoints provide ongoing technical support after the sale.
WPS in Action
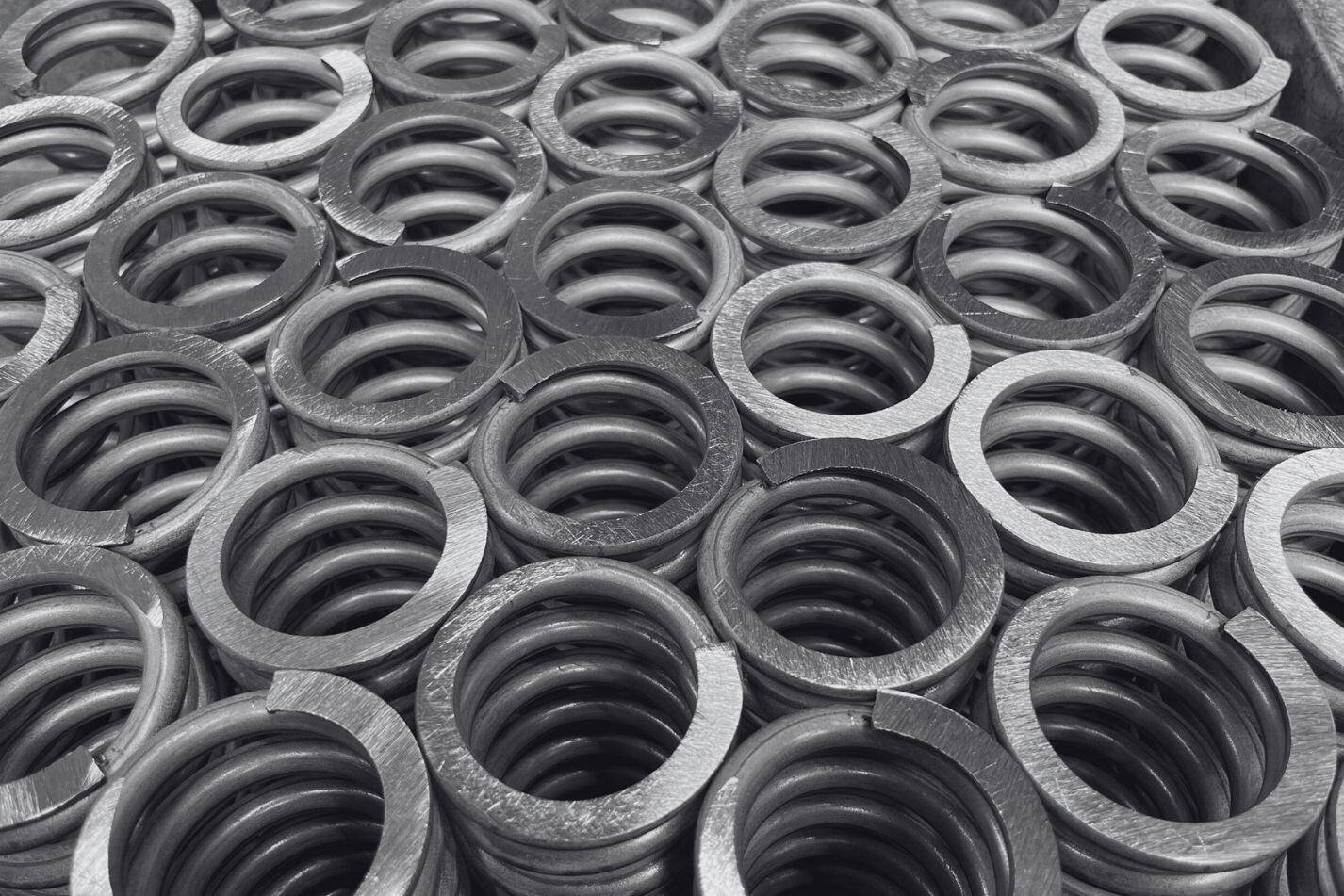
Spring End Grinding White paper
Find out how to optimize your spring end grinding by enhancing quality and efficiency in just 5 steps.
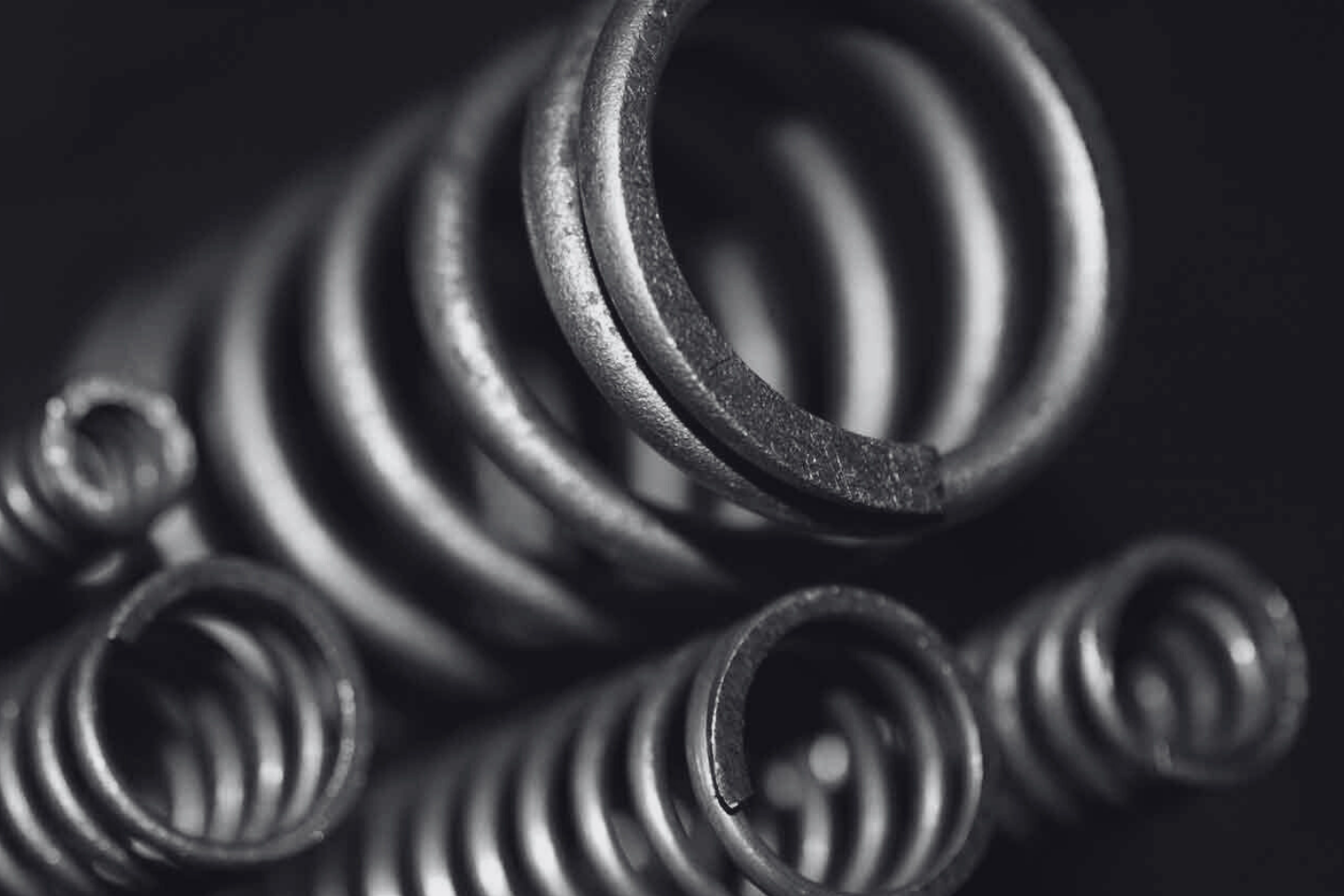
Spring End Grinding Case Study
Find out how our experts helped a spring producer boost their spring end grinding efficiency by 154%.
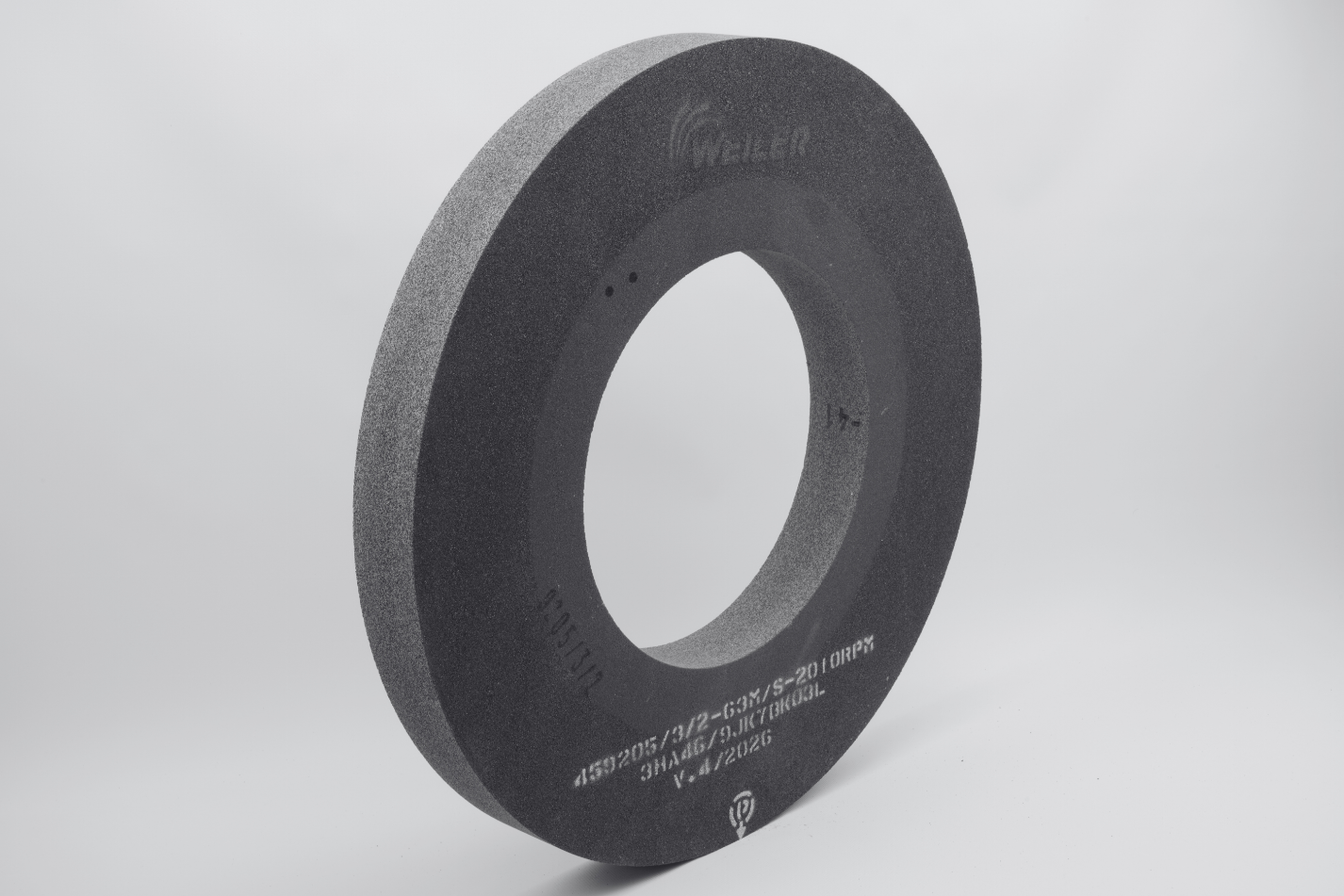
Roll grinding Case Study
Find out how our roll grinding technology helped a hot mill roll grinding facility reduce annual abrasives consumable cost by 45,77%.
The WCP Program Brings Real Value to Our End Users
"I consider Weiler to be a long-term partner. Their history of meeting our specific application needs has been world-class."
General Manager, Rolling Operations
Speak with an Expert
Weiler Abrasives is an industry leader and global manufacturer of surface conditioning solutions. We are eager to create a collaborative partnership to overcome your toughest cleaning, grinding, cutting, de-burring, and finishing challenges.