4 Tipps Zur Optimierung Der Qualität Und Zur Reduzierung Der Zykluszeit Beim Schleifen Von Zahnradprofilen
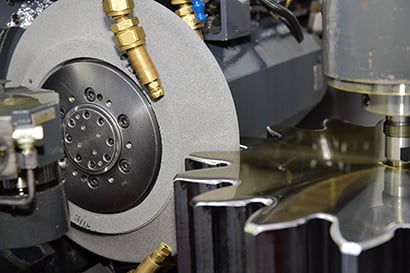
Das Profilschleifen bietet Vielseitigkeit und kann bei Zahnrädern mit Platzproblemen eingesetzt werden, die andere Schleifverfahren nicht zulassen.
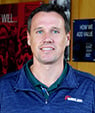
Author:
Dennis Brown,
Technischer Vertriebsleiter,
Weiler Abrasives
Steigern Sie Ihre Wettbewerbsfähigkeit Durch Prozessverbesserungen:
Das Schleifen von Zahnradprofilen, auch als Formschleifen bekannt, ist ein Fertigungsverfahren, das in der Zahnradherstellung verwendet wird. Dabei werden keramisch gebundene Schleifscheiben verwendet, um das Profil einer Verzahnung zu ändern oder zu korrigieren, oft nach einer Wärmebehandlung. Die Schleifscheibe läuft zwischen zwei gegenüberliegenden Zähnen und schleift beide Oberflächen gleichzeitig.
Im Vergleich zum Zahnradschneiden bietet dieses Verfahren eine genauere Zahnoberfläche und ist vielseitiger, da es ermöglicht, ein spezifisches, einzigartiges Profil zu erstellen oder Profilkorrekturen vorzunehmen, indem eine Schleifscheibe verwendet wird, die für die erforderlichen Korrekturen oder Modifikationen abgerichtet ist. In den meisten Anwendungen kommt eine Typ-1- oder Typ-4-Scheibe zur Anwendung. Die Maschine und die Verzahnungsgeometrie bestimmen die Größe der Scheibe.
Profilschleifen wird verwendet, um interne und externe Verzahnungen zu schleifen und bietet eine einzigartige Vielseitigkeit. Es kann bei Zahnrädern verwendet werden, bei denen Platzprobleme andere Schleifprozesse wie das kontinuierliche Wälzschleifen nicht zulassen. Typischerweise wird das Profilschleifen verwendet, um größere Zahnräder mit Modul größer als 5 zu bearbeiten. Mit dieser Art des Schleifens werden viele Arten von Zahnrädern in verschiedenen Branchen hergestellt – von der Automobil- und Luftfahrtindustrie bis hin zur Landwirtschaft und Energieerzeugung. Die Zahnräder können für einige Anwendungen ziemlich groß sein, wie zum Beispiel jene für den Bergbau und das Zerkleinern von Gestein, die über 10 m Durchmesser aufweisen. Die Methode hat sich jedoch auch bei kleineren Modulen als erfolgreich erwiesen, insbesondere wenn die Verzahnungsqualität entscheidend ist oder wenn spezielle Kleinserienproduktionen für F&E durchgeführt werden.
Aufgrund der hohen Qualitätsanforderungen kann das Profilschleifen ein sehr arbeits- und kostenintensiver Prozess sein, weshalb es für einen Hersteller ein wesentlicher Schritt in der Zahnradproduktion ist. Daher ist es wichtig, die richtige Schleifscheibe auszuwählen und Best Practices zu befolgen, die dazu beitragen, die Zykluszeit zu verkürzen, das Schleifbrand-Risiko zu verringern und die erzeugte Qualität des Verfahrens zu optimieren.
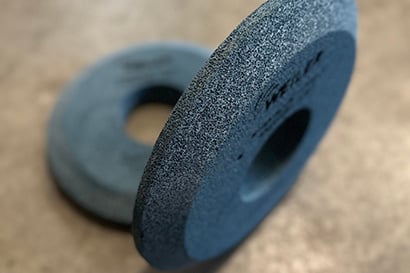
Einige Profilschleifscheiben werden vom Hersteller vorgeformt geliefert, wie dieses Beispiel einer leistungsstarken Profilschleifscheibe von Weiler Abrasives zeigt.
Grundlagen Des Profilschleifens
Das Schleifen des Zahnradprofils ist ein diskontinuierlicher Prozess, der die rechten und linken Zahnflanken gleichzeitig, Lücke für Lücke, schleift. Die Schleifscheibe wird mit den genauen Abmessungen des zu schleifenden Zahnrads abgerichtet. Die meisten Maschinen verwenden einen rotierenden Diamantabrichter, der entweder hinter der Schleifscheibe, auf der Scheibe oder darunter montiert ist. Während des Prozesses bewegen sich der Abrichter und die Schleifscheibe (oder eine Kombination aus beiden) in mehreren Achsen, um das gewünschte Zahnprofil zu erzeugen. Im Vergleich zum kontinuierlichen Wälzschleifen, bei der die erzeugende Bewegung das Profil herstellt, wird in diesem Prozess das Profil durch die Profilform erzeugt, mit der die Schleifscheibe abgerichtet ist. Dies trägt zu einer größeren Profilgenauigkeit bei.
Meistens ist das Zahnradschleifen der letzte Schritt im Herstellungsprozess. Nach dem Schleifen wird das Zahnrad in der Regel für die Montage vorbereitet. Die in diesem Prozess verwendeten Maschinen variieren je nach Hersteller und Größe. Einige Maschinen sind in der Lage, Zahnräder mit einem Durchmesser von bis zu 6 m innerhalb eines Gehäuses zu schleifen. Andere Maschinen sind für größere Produktionschargen gebaut und können mit automatischen Be- und Entladeeinrichtungen ausgestattet werden, obwohl der Materialtransport in und aus der Schleifmaschine typischerweise manuell mit Hebezeugen durchgeführt wird.

Eine leistungsstarke Profilschleifscheibe von Weiler Abrasives, mit hoher Porosität. Diese leistungsstarken Schleifscheiben bieten eine bessere Formhaltung und eine längere Standzeit.
Herausforderungen Beim Profilschleifen
Es gibt mehrere Faktoren, welche die Zykluszeit und die Qualität beim Profilschleifen beeinflussen können. Diese beinhalten:
- Schleifbrand: Das Vermeiden von Schleifbrand ist normalerweise das entscheidendste Qualitätsmerkmal beim Profilschleifen.
- Wenn Schleifbrand auftritt, kann er zu Ausschuss und längeren Zykluszeiten führen.
- Formhaltung: Die Fähigkeit der Schleifscheibe, die Form zu halten, ist das nächstwichtigste Qualitätsmerkmal und hat direkten Einfluss auf die Zykluszeit und die Verzahnungsgeometrie.
- Fähigkeitsniveau des Maschinenbedieners: Es ist entscheidend, dass der Bediener Kenntnisse über Zahnräder und eine Maschinenschulung im Profilschleifen hat. Das Finden, Schulen und Halten dieser Bediener kann eine Herausforderung sein.
- Standzeit der Schleifscheibe: Es ist wichtig, eine Schleifscheibe auszuwählen, die alle Qualitätsanforderungen erfüllt und gleichzeitig die längsmögliche Standzeit bietet. Die Verwendung der richtigen Schleifstrategie kann helfen, die Standzeit der Scheibe zu verlängern. D Aus diesem Grund sind Anwendungsschulungen für Bediener von Profilschleifmaschinen besonders wichtig, um sicherzustellen, dass sie die richtigen Schleifstrategien anwenden.
- Falsche Parameter: Zuerst muss die grundsätzliche Schleifstrategie festgelegt werden, dann können die Maschinenparameter programmiert oder angepasst werden. Die Verwendung falscher Programmierparameter im Profilschleifprozess kann zu längeren Zykluszeiten, schlechter Zahnradqualität, Schleifbrand und erhöhtem Ausschuss in der Zahnradproduktion führen. Die Beratung durch einen Anwendungstechniker, beispielsweise von einem Schleifmittelhersteller wie Weiler Abrasives, kann die Ergebnisse verbessern.
-
Produktionsengpässe: Der Profilschleifprozess kann eine Quelle für Engpässe sein. Bei sehr großen Zahnrädern oder beim Tiefschleifen kann die Zykluszeit zum Beispiel zwei bis zwölf Stunden betragen. Eine strategische Änderung an der Schleifscheibe selbst oder eine Parameteranpassung kann diese Zeit möglicherweise um die Hälfte oder mehr verkürzen.
Produktoptionen Bei Der Auswahl Von Schleifmitteln
Bei der Auswahl einer Schleifscheibe stehen viele Bindungsformeln zur Verfügung. Je nach Härte, Größe und Fertigungsmethode des Zahnrads werden verschiedene Schleifscheiben unterschiedliche Ergebnisse liefern. Weitere zu berücksichtigende Faktoren sind die Größe der Schleifscheibe (Breite und Durchmesser) sowie die Nenngeschwindigkeit. Verschiedene Arten von Schleifscheiben können unterschiedliche Schneideigenschaften, Haltbarkeit und Produktlebensdauer bieten.
Typischerweise fällt die Wahl beim Profilschleifen auf eine Schleifscheibe mit hoher Porosität, mit keramischem Bindungssystem und entweder Aluminiumoxidkörner oder Hochleistungskeramikkörner. Dies unterscheidet sich von den Scheiben, die beim kontinuierlichen Wälzschleifen verwendet werden, bei denen typischerweise eine Schleifscheibe mit normaler oder nicht-induzierter Porosität zum Einsatz kommt. Für das Profilschleifen wird vorzugsweise eine Scheibe mit induzierter Porosität oder sehr großen Poren verwendet, um das Risiko einer Beschädigung oder eines Verschrottens des Werkstücks zu verringern, was den Arbeitsvorgang erheblich verteuern kann - es ist wichtig, die richtige Scheibe für die jeweilige Aufgabe zu verwenden. Selbst wenn die Schleifscheibe nicht mit ihrer größten Auslastung genutzt wird, kann die Auswahl der richtigen Scheibe dazu beitragen, katastrophale Folgen zu vermeiden. Eine falsche Schleifscheibe kann ein Unternehmen potenziell Tausende von Euros oder mehr kosten, wenn das gefertigte Zahnrad nach der Installation und Inbetriebnahme ausfällt.
Suchen Sie sich einen Schleifmittelhersteller, der Ihre Anwendungsanforderungen beurteilen und eine Schleifscheibe für das Profilschleifen herstellen kann, die eine optimierte Leistung erbringt. Ein Qualitätshersteller kann maßgeschneiderte Schleifscheiben mit verschiedenen Schleifkorngrößen und -Arten entwickeln, die auf die Verwendung mit einer Vielzahl von CNC-Maschinen angepasst sind.
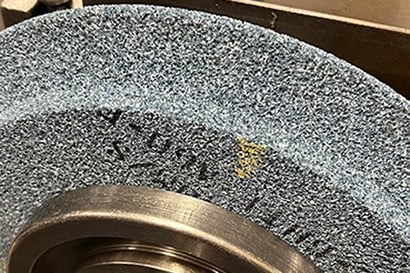
Eine offenporige, keramisch gebundene Schleifscheibe verwendet entweder Aluminiumoxidkörner oder Hochleistungskeramikkörner. Für das Profilschleifen ist es vorzuziehen, eine Schleifscheibe mit induzierter Porosität oder sehr großen Poren zu verwenden, um das Risiko einer Beschädigung oder Verschrottung des Werkstücks zu verringern. Dieses Bild zeigt eine offenporige Schleifscheibe nach dem Schleifen ohne Anzeichen von Beanspruchung.
4 Tipps Für Das Profilschleifen
Qualitätsoptimierung und Reduzierung der Zykluszeit beim Profilschleifen erfordern die Beachtung einiger wichtiger Best Practices. Auch die Schleifstrategie spielt eine entscheidende Rolle. Berücksichtigen Sie also Faktoren wie „Wie viele Zähne können wir schleifen, bevor wir abrichten müssen?“ Behalten Sie diese vier Tipps für das Profilschleifen im K
1. Bessere Formhaltung:
Es gibt zwei Elemente im Schleifzyklus zu berücksichtigen: die Schleifzeit und die Abrichtzeit. Die Abrichtzeit zwischen den Schleifzeiten kann drei bis acht Minuten oder mehr betragen. Daher gilt: Je besser die Form gehalten werden kann, desto länger können Sie zwischen den Abrichtzyklen schleifen und desto kürzer wird Ihre Zykluszeit sein. Daher sind Anwenderschulungen für Bediener von Profilschleifmaschinen besonders wichtig, um sicherzustellen, dass sie die richtigen Schleifstrategien verwenden. Wenden Sie sich an einen Schleifmittelhersteller, um eine Schleifscheibe mit optimaler Körnung und Bindungssystem zur Maximierung der Formhaltung zu erhalten.
2. Geringere Schleiftemperatur:
Das wichtigste Qualitätsmerkmal beim Profilschleifen ist das Vermeiden von Schleifbrand. Schleifbrand tritt auf, wenn die Zahnoberfläche sehr hohen Temperaturen aus dem Schleifprozess ausgesetzt wurde. Dies kann die Härte verringern und Spannungen im Zahnradmaterial verursachen, was zu Rissen führt, die später einen Ausfall des Zahnrades zur Folge haben. Die meisten Maschinen verfügen über Kühlsysteme mit hohem Durchfluss, die ausreichende Spüleigenschaften bieten, um die vom Schleifrad erzeugten Metallspäne wegzuspülen, sowie über Hochdruckdüsen, um die Scheibe zu reinigen. Bevor eine Schleifscheibe ausgewählt werden kann, müssen diese Bedingungen erfüllt sein, sonst wird die Scheibe nicht wie vorgesehen funktionieren. Eine Schleifscheibe, die bei geringeren Temperaturen schleift, kann zahlreiche Vorteile bieten. Wenn Sie die Zerspanleistung der Scheibe erhöhen, ist es wichtig, eine Schleifscheibe mit geringerer Schleiftemperatur zu wählen, um Schleifbrand am Bauteil und mögliches Ausfallen der Scheibe zu vermeiden. Die Schleiftemperatur wird dadurch geringer, dass die Schleifkörner genau zum richtigen Zeitpunkt aus der Bindung brechen und dadurch, dass die zur Aufgabe passende Körnung verwendet wird. Wenn eine Hochleistungsschleifscheibe kühler schleift, kann sie möglicherweise auch schneller schleifen. Darüber hinaus wird das Risiko von Qualitätsmängeln verringert und der Schleifvorgang stabilisiert, wenn die Rohbearbeitung des Zahnrads vor dem Schleifen so genau wie möglich oder in optimaler Geometrie und Größe erfolgt.
3. Standzeit der Scheibe mit höheren Zerspanungsvolumina (V’w) erhöhen:
Das Zerspanungsvolumen ist das Maß dafür, wie viel Zahnradmaterial entfernt werden kann, bevor die Geometrie korrigiert werden muss, was auch als Formverlust bezeichnet wird. Wenn eine Maschine eingerichtet wird, wird die Form in die Schleifscheibe abgerichtet und das Zahnrad wird geschliffen — so befindet sich die Form auf dem Zahnrad. Die gleiche Form auf der Schleifscheibe wird auf das Zahnrad übertragen.
Wie oft dies geschehen kann, bevor die Form außerhalb der Toleranz oder unakzeptabel ist, wird als erreichbares Zerspanungsvolumen bezeichnet, das durch eine volumetrische Berechnung ermittelt wird. Denken Sie daran, die Abrichtzeit kann mehrere Minuten betragen; daher kann eine Reduzierung der Zykluszeit durch eine optimale Schleif- und Abrichtstrategie erreicht werden. Unterschiedliche Schleifscheiben haben unterschiedliche Zerspanungsvolumina. Generell haben kostengünstige Schleifscheiben ein geringeres Zerspanungsvolumen , während Hochleistungsscheiben ein sehr hohes Zerspanungsvolumen aufweisen. Höhere Zerspanungsvolumina führen zu einer längeren Standzeit der Scheibe und zu einer geringeren Zykluszeit.
Diese wird erreicht, indem die Anzahl der Abrichtintervalle reduziert wird. Wenn die Schleifstrategie korrekt und optimiert ist, erzielen Sie das beste Ergebnis mit einer Hochleistungsscheibe.
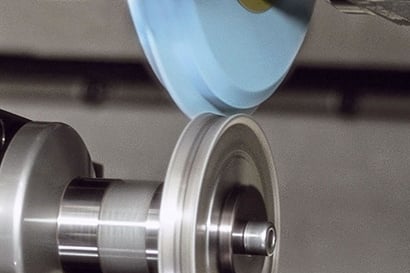
Abrichten einer Profilschleifscheibe, um die verwendete Methode zu demonstrieren.
4. Zykluszeit mit hohen Materialabtragsraten (Q’w) verringern:
Eine Erhöhung der Materialabtragsrate (MRR) verringert die Zykluszeit. Die Materialabtragsrate ist ein Maß dafür, wie schnell die Schleifscheibe Material vom Werkstück entfernt. Je höher der Wert, desto höher die Abtragsrate. Eine höhere MRR kann entweder durch Erhöhung des Materialabtrags oder durch Erhöhung der Vorschubrate der Scheibe erzielt werden – oder durch eine Kombination von beidem. Die Formel für Q’w lautet:
′w = ( * )/60
wobei,
= Materialabtrag, in Volumeneinheiten
= Vorschubrate, Einheiten in Weg / Zeit
Abhängig von der verwendeten Schleifscheibentechnologie kann eine hohe Vorschubrate einer niedrigen Vorschubrate mit hohem Materialabtrag vorgezogen werden. Dies ist ein bedeutender Faktor beim Schleifen und meist eine der ersten Fragen, die von Bedienern gestellt werden. Die Q’w-Formel zeigt, dass Sie die Materialabtragsrate anpassen können, indem Sie die richtige Schleifscheibentechnologie einsetzen, um den Materialabtrag, die Vorschubgeschwindigkeit oder beides zu optimieren. Es ist wichtig zu beachten, dass Zahnräder mit einer geringen Zähnezahl entlang des Profils vom Fuß bis zum Kopf ein variables Q’w aufweisen. Da der Profilwinkel bei mittleren bis großen Teilungen vom Fuß bis zum Kopf variiert, erfordert dieser Zahnradtyp eine andere Schleifstrategie, um Qualität zu erzielen und Schleifbrand zu verhindern. Wie andere Elemente des Schleifprozesses wird auch Q’w vom Kühlsystem, der Verzahnungsgeometrie und weiteren Faktoren beeinflusst. Beachten Sie auch, dass eine Erhöhung der Abtragsrate mittels der Vorschubrate zusätzliche Belastungen für die Maschine verursachen und zu vorzeitigen Maschinenausfällen führen kann, was Wartungs- und Stillstandszeiten erhöht.
Qualität und Effizienz sind beim Profilschleifen entscheidend. Ein Anwendungsingenieur für Zahnräder kann eine Schleifstrategie für ein bestimmtes Zahnrad entwerfen, bevor die Maschine außer Betrieb genommen und eingerichtet wird. Die Zusammenarbeit mit einem Anwendungsingenieur eines Schleifscheibenherstellers liefert dem Bediener oder Einrichter wertvolle Informationen, um das Schleifprogramm mit optimalen Schleifraten und Zerspanvolumina für die vorgeschlagene Schleifscheibentechnologie zu entwerfen. Sie können auch feststellen, ob die Schleifscheibentechnologie korrekt ist oder ob sie neugestaltet oder geändert werden muss. Hersteller möchten kosteneffizient sein und die Zykluszeit beim Profilschleifen reduzieren, müssen aber vor allem eine extrem hohe Qualität erhalten, was eine Zyklusvorhersage durch die Programmierung entscheidend macht. Der richtige Schleifscheibenhersteller versteht diese Herausforderungen und kann mit Bedienern und Ingenieuren zusammenarbeiten, um die Schleifscheibe zu konzipieren, die am besten geeignet ist – um Kosten zu sparen und die Zykluszeit zu optimieren, ohne die Qualität zu beeinträchtigen.