Spring End Grinding Case Study Innovative Grinding Solution Streamlines Spring Production
The Challenge:
Facing the task of enhancing production efficiency, a German manufacturer of springs and metallic components wanted to eliminate the need for multiple grinding wheels when grinding spring ends of different wire materials. The requirement was to find a single grinding solution for high carbon steel 4,0 mm and stainless steel 3,6 mm compression springs, thus streamlining their manufacturing process and meeting increased market demands.
The Solution:
The journey to optimization began with an initial consultation with the customer, who expressed the need for a universal spring-end grinding wheel. Weiler Abrasives’ experts proposed the 36/22 450x80x100 mm ICE Spring VA24 BA20 wheel would fit the client’s requirements. As part of the Weiler Process Solutions (WPS) program, Weiler Abrasives conducted a detailed evaluation of the ICE Spring grinding wheel’s capabilities, focusing exclusively on a singular machine type to ensure precision and consistency. This critical step involved adjusting the grinding process, particularly optimizing grinding cycle times to shorten the entire grinding process and carefully calibrating dressing parameters to enhance the wheel’s efficiency and lifespan.
The testing sequence began with trials on stainless steel, followed by high-carbon steel. This strategic approach within the WPS framework ensured that the ICE Spring wheel was tested and refined under actual production conditions, confirming its versatility and superior performance across different steel types.
The Results:
The outcome of the comprehensive testing supported by the extensive and in-depth industry knowledge of our experts was impressive:
- Grinding Time Reduction:
- Stainless Steel: from 2.00 min to 1.31 min, representing a reduction of 24,17 %.
- High Carbon Steel: from 2,20 min to 2,00 min, representing a reduction of 14,29 %.
- Decrease in Dressing Frequency: from 4 cycles to an impressive 8,5 cycles, representing a 112,5 % improvement in durability and operational efficiency.
- Extended Wheel Life:
- Stainless Steel: ICE Spring has ground 98.830 springs per wheel compared to 68.921 by the competitor for a 43,40% boost in efficiency.
- High Carbon Steel: ICE Spring has ground 167.482 springs per wheel compared to 139.568 by the competitor for a 20% boost in efficiency.
- Labor Cost Savings:
- Stainless Steel: 28,38% reduction in labor cost per cycle, from 2,29 € to 1,64 €.
- High Carbon Steel: 25,23% reduction in labor cost per cycle, from 2,18 € to 1,63 €.
The Optimal Solution for All Spring Types: The ICE Spring Advantage
The ICE Spring wheel showcased unparalleled versatility, designed to handle a wide range of wire materials with a single solution. This breakthrough simplifies production processes, reflecting our dedication to innovation and the diverse requirements of the spring manufacturing industry.
Conclusion
Leveraging the ICE Spring wheel's universal capabilities, Weiler Abrasives has set new benchmarks in manufacturing efficiency and adaptability. Our approach, tailored to understand and meet the diverse needs of our clients, consistently delivers superior results. Highlighting our dedication to innovation and excellence, this narrative showcases the significant industry advancements achieved through our collective expertise. Embracing cutting-edge technology and collaborative efforts, we open a world of possibilities, nurturing a culture where continuous improvement and mutual success are paramount.
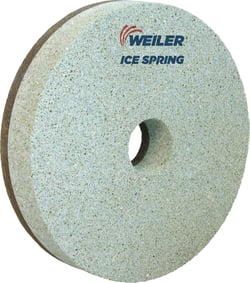